Hipfiring: The Ultimate Guide To Understanding And Mastering This Revolutionary Technology
Mar 24 2025
Hipfiring has become one of the most talked-about topics in recent years, particularly within the realms of technology, engineering, and innovation. This term refers to a process that significantly enhances the performance and durability of various materials. Whether you're a researcher, engineer, or simply someone interested in cutting-edge technology, understanding hipfiring is essential. This article will provide a comprehensive overview of hipfiring, including its definition, applications, benefits, and more.
Hipfiring is not just a buzzword; it represents a groundbreaking advancement in materials science. Its applications span across multiple industries, from aerospace to automotive manufacturing. By the end of this article, you'll gain a deeper understanding of how hipfiring works, its significance, and why it's transforming the way we approach material development.
As we delve deeper into the world of hipfiring, it's important to note that this process is backed by extensive research and supported by leading experts in the field. Our goal is to provide you with a resource that is not only informative but also actionable, helping you make informed decisions about incorporating hipfiring into your projects.
Table of Contents
- What is Hipfiring?
- The Hipfiring Process
- Applications of Hipfiring
- Benefits of Hipfiring
- Challenges in Hipfiring
- The History of Hipfiring
- Hipfiring vs. Traditional Methods
- Impact on Various Industries
- Future Trends in Hipfiring
- Conclusion
What is Hipfiring?
Hipfiring is a specialized technique used in the manufacturing of advanced materials. It involves the application of high-pressure and high-temperature conditions to compact powders into dense, solid materials. This process is particularly effective for producing ceramics and metal-ceramic composites with superior mechanical properties.
The term "hipfiring" is derived from the combination of "hot isostatic pressing" (HIP) and firing processes. By combining these techniques, manufacturers can achieve materials with enhanced strength, durability, and resistance to wear and corrosion.
This technology has gained significant attention due to its ability to address the limitations of conventional manufacturing methods. As industries continue to demand stronger and more reliable materials, hipfiring offers a solution that meets these requirements.
Key Components of Hipfiring
- High-temperature application
- High-pressure environment
- Powder compaction
- Material densification
The Hipfiring Process
The hipfiring process involves several critical steps that ensure the production of high-quality materials. These steps are carefully controlled to achieve optimal results. Below is a detailed breakdown of the process:
Step 1: Material Preparation
Before the hipfiring process begins, the raw materials must be carefully prepared. This involves selecting the appropriate powders and ensuring they meet the required specifications. The powders are then placed into a mold or container designed to withstand the high-pressure and high-temperature conditions.
Step 2: Application of Pressure and Heat
Once the materials are prepared, they are subjected to high-pressure and high-temperature conditions. This step is crucial as it allows the powders to compact and densify, forming a solid material with enhanced properties. The pressure and temperature levels are carefully controlled to ensure uniform compaction and minimize defects.
Step 3: Cooling and Post-Processing
After the hipfiring process is complete, the material is cooled gradually to prevent thermal shock. Post-processing steps may include machining, finishing, and quality control inspections to ensure the final product meets the desired specifications.
Applications of Hipfiring
Hipfiring finds applications in a wide range of industries due to its ability to produce materials with exceptional properties. Some of the key industries that benefit from hipfiring include:
- Aerospace: Hipfiring is used to manufacture lightweight and high-strength components for aircraft engines and structural parts.
- Automotive: The automotive industry utilizes hipfiring to produce components such as brake discs and engine parts that require superior wear resistance.
- Medical: Hipfiring is employed in the production of biocompatible materials for implants and prosthetics.
- Energy: This technology is used in the development of materials for nuclear reactors and other energy-related applications.
Benefits of Hipfiring
Hipfiring offers numerous advantages over traditional manufacturing methods. Some of the key benefits include:
- Improved Mechanical Properties: Materials produced through hipfiring exhibit enhanced strength, toughness, and resistance to wear and corrosion.
- Uniform Material Structure: The high-pressure and high-temperature conditions ensure uniform compaction, resulting in materials with consistent properties.
- Cost-Effective: Although the initial investment in hipfiring equipment can be high, the process reduces material waste and improves production efficiency, leading to long-term cost savings.
Challenges in Hipfiring
Despite its numerous benefits, hipfiring is not without its challenges. Some of the key challenges include:
- High Initial Costs: The equipment required for hipfiring is expensive, which can be a barrier for smaller manufacturers.
- Complexity of Process: The hipfiring process requires precise control of temperature and pressure, making it complex and demanding for operators.
- Material Limitations: Not all materials are suitable for hipfiring, which limits its application in certain industries.
The History of Hipfiring
The concept of hipfiring dates back to the mid-20th century when researchers began exploring the potential of combining hot isostatic pressing with firing processes. Over the years, advancements in technology and materials science have refined the process, making it more efficient and versatile.
Today, hipfiring is recognized as a critical technology in the development of advanced materials. Its evolution reflects the ongoing efforts of scientists and engineers to push the boundaries of what is possible in materials manufacturing.
Hipfiring vs. Traditional Methods
When compared to traditional manufacturing methods, hipfiring offers several advantages. While conventional techniques such as sintering and casting can produce high-quality materials, they often fall short in terms of achieving uniform material properties and minimizing defects.
Hipfiring addresses these limitations by providing a more controlled and precise manufacturing process. This results in materials with superior performance characteristics, making hipfiring the preferred choice for many applications.
Impact on Various Industries
The impact of hipfiring on various industries is significant. From aerospace to healthcare, this technology is transforming the way materials are developed and utilized. Below are some examples of how hipfiring is influencing different sectors:
Aerospace Industry
In the aerospace industry, hipfiring is used to produce lightweight and high-strength components that are essential for modern aircraft. These components contribute to improved fuel efficiency and reduced environmental impact.
Medical Industry
The medical field benefits from hipfiring through the production of biocompatible materials for implants and prosthetics. These materials offer improved durability and compatibility with the human body, enhancing patient outcomes.
Future Trends in Hipfiring
As technology continues to advance, the future of hipfiring looks promising. Researchers are exploring new materials and processes to further enhance the capabilities of this technology. Some of the emerging trends include:
- Development of New Materials: Scientists are investigating the use of advanced ceramics and composites in hipfiring to expand its applications.
- Automation and AI Integration: The integration of automation and artificial intelligence in the hipfiring process is expected to improve efficiency and reduce costs.
- Sustainability Focus: There is a growing emphasis on developing hipfiring processes that are environmentally friendly and sustainable.
Conclusion
Hipfiring represents a revolutionary advancement in materials science, offering a solution to many of the challenges faced by traditional manufacturing methods. Its ability to produce materials with superior mechanical properties makes it an invaluable technology across various industries.
As we continue to explore the potential of hipfiring, it is essential to stay informed about the latest developments and trends. We encourage you to share your thoughts and experiences with hipfiring in the comments section below. Additionally, don't forget to explore other articles on our website for more insights into cutting-edge technologies and innovations.
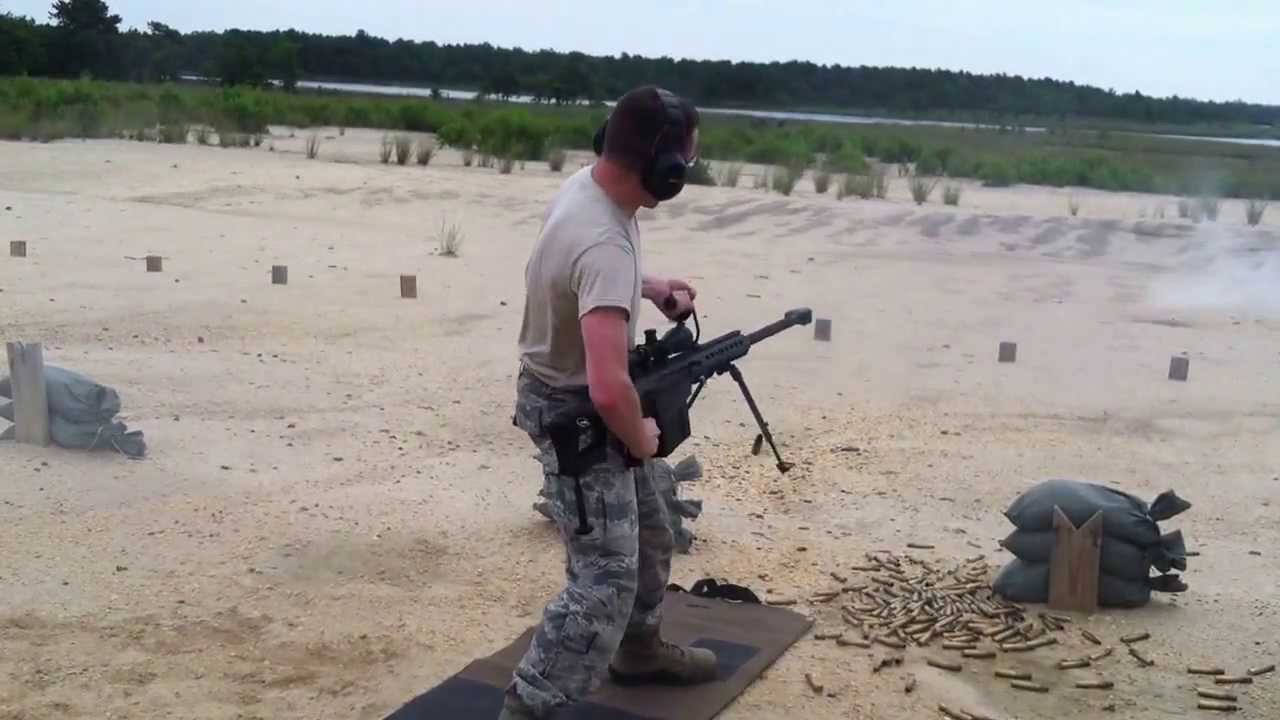
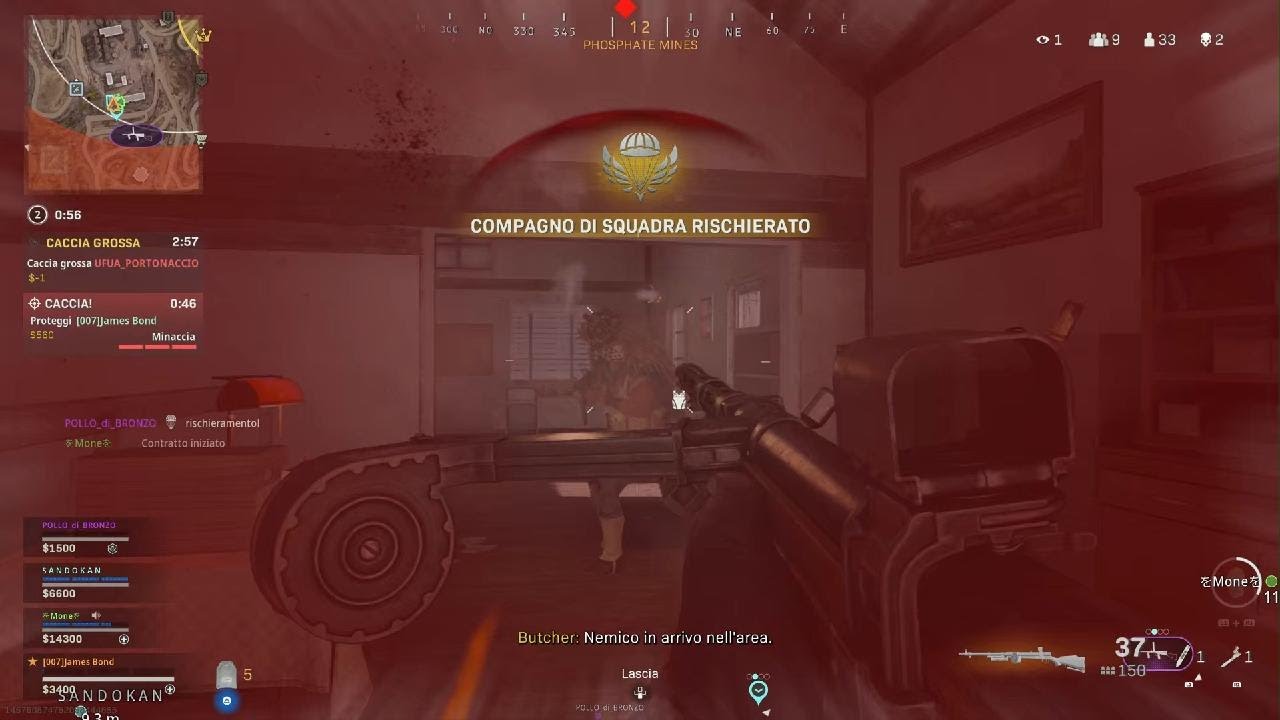
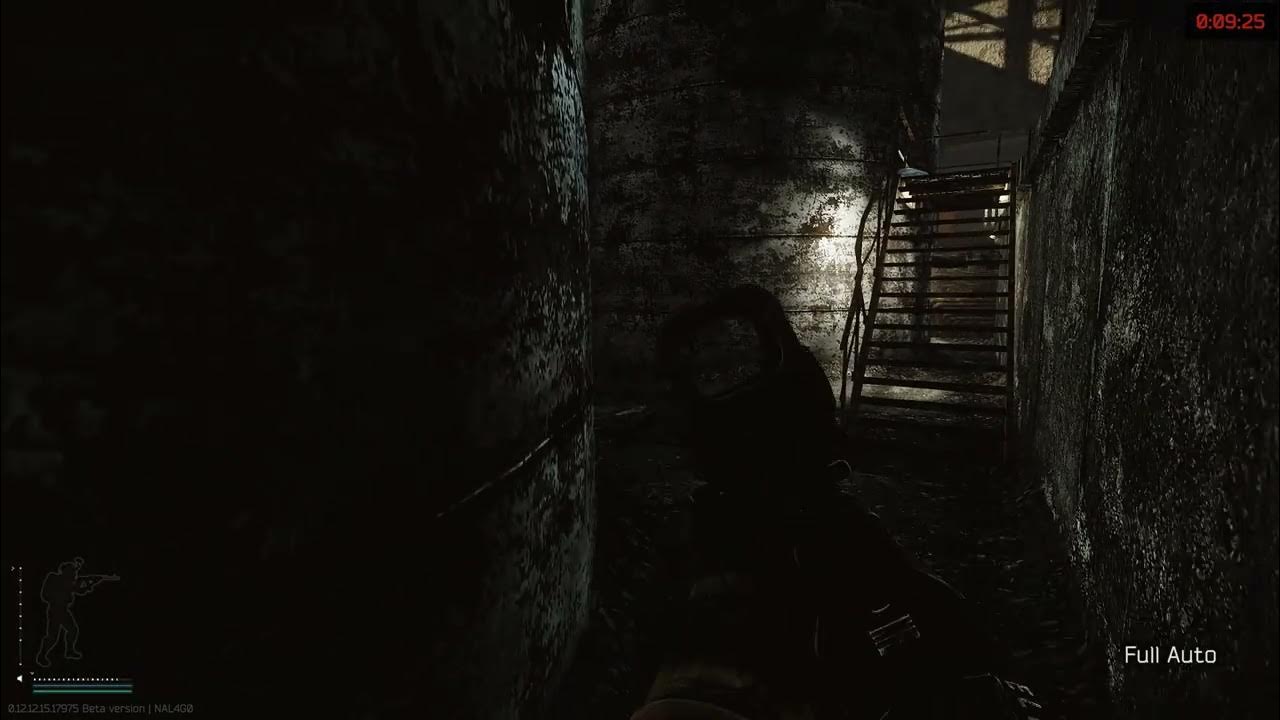