Magnesium parts are typically attached using specific methods and materials designed to ensure durability, strength, and reliability in various applications. Magnesium, known for its lightweight properties, is increasingly used in industries such as automotive, aerospace, and electronics. However, attaching magnesium components requires specialized techniques to maintain structural integrity and performance.
As technology advances, the demand for efficient and effective methods to attach magnesium parts has grown significantly. Manufacturers are constantly exploring new ways to enhance the attachment process while ensuring safety and compliance with industry standards. Understanding the techniques and materials involved is crucial for engineers, designers, and professionals working in this field.
This article will delve into the various methods used to attach magnesium parts, including welding, adhesive bonding, mechanical fastening, and brazing. Additionally, we will explore the advantages, disadvantages, and best practices associated with each technique. By the end of this guide, you will have a comprehensive understanding of the most effective methods for attaching magnesium components.
Table of Contents
- Biography of Magnesium in Engineering
- Overview of Magnesium Attachment Methods
- Welding Magnesium Parts
- Adhesive Bonding Techniques
- Mechanical Fastening Methods
- Brazing Magnesium Components
- Advantages and Disadvantages of Each Method
- Applications of Magnesium Attachment
- Industry Standards and Regulations
- Future Trends in Magnesium Attachment
- Conclusion
Biography of Magnesium in Engineering
Magnesium is a versatile material with a long history in engineering and manufacturing. It is the lightest structural metal available, making it ideal for applications where weight reduction is critical. Below is a brief overview of magnesium's properties and its significance in modern engineering:
Property | Value |
---|---|
Atomic Number | 12 |
Atomic Weight | 24.305 g/mol |
Density | 1.74 g/cm³ |
Melting Point | 650°C |
Thermal Conductivity | 156 W/m·K |
Magnesium's lightweight nature and excellent strength-to-weight ratio make it a preferred choice for industries seeking to reduce fuel consumption and improve efficiency.
Overview of Magnesium Attachment Methods
Magnesium parts are typically attached using a variety of methods, each suited to specific applications and requirements. The choice of method depends on factors such as the environment, load conditions, and material compatibility. Below are the primary methods used:
Common Techniques
- Welding
- Adhesive bonding
- Mechanical fastening
- Brazing
Each technique offers unique advantages and challenges, which will be explored in detail in the following sections.
Welding Magnesium Parts
Welding is a popular method for attaching magnesium components due to its ability to create strong, permanent joints. However, welding magnesium requires specialized skills and equipment to prevent issues such as cracking and porosity.
Types of Welding
- Tungsten Inert Gas (TIG) Welding
- Metal Inert Gas (MIG) Welding
- Laser Welding
According to a study published in the Journal of Materials Science, TIG welding is particularly effective for magnesium due to its precise control and minimal heat input. This reduces the risk of distortion and ensures high-quality welds.
Adhesive Bonding Techniques
Adhesive bonding is another widely used method for attaching magnesium parts. It offers several advantages, including reduced weight, improved fatigue resistance, and enhanced aesthetics. However, selecting the right adhesive is crucial for achieving optimal performance.
Popular Adhesives
- Epoxy
- Polyurethane
- Cyanoacrylate
A report from the American Society for Testing and Materials (ASTM) highlights the importance of surface preparation when using adhesives on magnesium. Proper cleaning and priming can significantly improve bond strength and durability.
Mechanical Fastening Methods
Mechanical fastening involves the use of screws, bolts, and rivets to attach magnesium parts. This method is favored for its simplicity and ease of disassembly. However, it requires careful consideration of material compatibility and stress distribution.
Types of Fasteners
- Self-tapping screws
- Huck bolts
- Blind rivets
Research conducted by the Society of Automotive Engineers (SAE) indicates that mechanical fastening is particularly effective for high-stress applications, such as automotive and aerospace components.
Brazing Magnesium Components
Brazing is a less common but highly effective method for attaching magnesium parts. It involves heating the components to a temperature below their melting point and using a filler metal to create a strong joint. Brazing is particularly useful for joining dissimilar materials.
Advantages of Brazing
- High-strength joints
- Excellent corrosion resistance
- Minimal distortion
A study published in the International Journal of Advanced Manufacturing Technology demonstrates the potential of brazing for magnesium components, especially in applications requiring high thermal conductivity.
Advantages and Disadvantages of Each Method
Each attachment method has its own set of advantages and disadvantages. Understanding these can help engineers make informed decisions based on their specific needs.
Comparison Table
Method | Advantages | Disadvantages |
---|---|---|
Welding | Strong, permanent joints | Risk of cracking and porosity |
Adhesive Bonding | Lightweight, improved aesthetics | Requires surface preparation |
Mechanical Fastening | Simple, easy to disassemble | Potential for stress concentration |
Brazing | High-strength joints, corrosion resistance | Complex setup, limited applications |
Applications of Magnesium Attachment
The methods used to attach magnesium parts find applications across various industries. Some of the most prominent sectors include:
Key Industries
- Automotive
- Aerospace
- Electronics
- Medical Devices
For example, in the automotive industry, magnesium components are often used in engine parts and structural components to reduce vehicle weight and improve fuel efficiency.
Industry Standards and Regulations
Adhering to industry standards and regulations is crucial when attaching magnesium parts. These standards ensure safety, reliability, and compliance with legal requirements. Some of the key standards include:
- ISO 9001: Quality Management Systems
- AS9100: Aerospace Quality Management Systems
- IATF 16949: Automotive Quality Management Systems
Manufacturers must ensure that their attachment methods meet these standards to avoid potential risks and liabilities.
Future Trends in Magnesium Attachment
As technology continues to evolve, new trends are emerging in the field of magnesium attachment. Advances in materials science, robotics, and automation are driving innovation and improving the efficiency of attachment processes.
Emerging Technologies
- Additive manufacturing
- Smart adhesives
- Hybrid joining techniques
A report from the National Institute of Standards and Technology (NIST) predicts that these technologies will play a significant role in shaping the future of magnesium attachment in various industries.
Conclusion
In conclusion, attaching magnesium parts requires careful consideration of the methods and materials used. Whether through welding, adhesive bonding, mechanical fastening, or brazing, each technique offers unique advantages and challenges. By understanding these factors, engineers and manufacturers can select the most appropriate method for their specific applications.
We encourage readers to share their thoughts and experiences in the comments section below. Additionally, feel free to explore other articles on our site for more insights into materials science and engineering practices. Together, we can continue to advance the field of magnesium attachment and drive innovation in various industries.

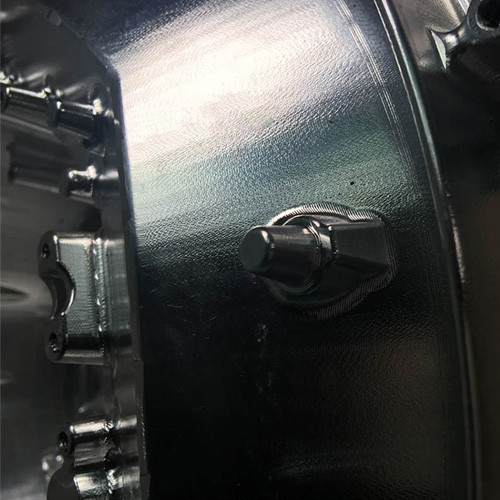
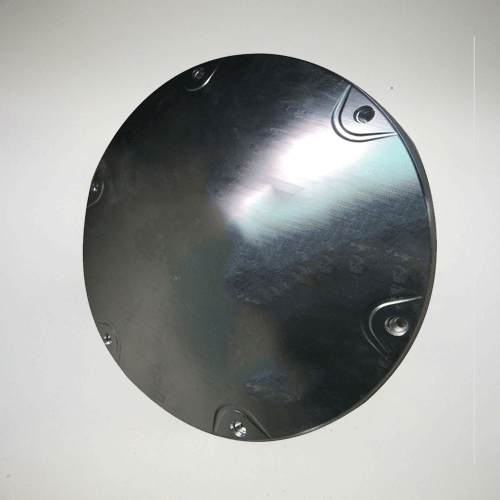